液态硅胶(LSR)技术近年来通过材料科学、工艺创新和智能化制造的深度融合,实现了从模具设计到终端应用的全链条升级。尤其在精密电子、医疗健康、新能源等领域的突破性应用,标志着LSR技术从“辅助材料”向“功能化核心组件”的跨越。以下是技术革新的关键路径和未来潜力分析:
一、模具制造:精度与效率的颠覆性突破
智能模具设计
AI驱动的模流仿真:通过机器学习算法优化模具流道设计,预测材料填充过程的气泡、缩痕等缺陷,良率提升30%以上(如Moldflow与LSR专用软件的深度结合)。
纳米级表面处理:采用类金刚石涂层(DLC)或微弧氧化技术,模具寿命延长5倍以上,同时实现LSR制品表面无痕脱模。
随形冷却水路:3D打印技术制造的异形冷却通道,使模具温度均匀性误差<±1℃,显著缩短成型周期。
柔性制造革命
模块化模具系统:针对多品种、小批量需求(如医疗器械),通过快速换模技术实现“一机多模”,切换时间缩短至10分钟内。
增材制造模具:金属3D打印的随形镶件,解决传统加工中无法实现的微流道(<0.2mm)和仿生结构。
二、材料创新:从性能增强到功能化
高性能配方突破
耐极端环境型LSR:耐温范围扩展至-60℃~300℃(如瓦克化学的SilGel®系列),耐受强酸、强碱和辐射环境。
导电/导热改性:添加氮化硼、碳纳米管等填料,导热率提升至5 W/m·K以上(如迈图的TC-5005),满足5G基站和电动汽车功率模块散热需求。
生物相容性与安全性
医疗级LSR:通过ISO 10993认证,用于长期植入器械(如心脏起搏器密封件),并开发抗菌型LSR(掺入银离子或光触媒材料)。
食品接触安全:符合FDA 21 CFR 177.2600标准,用于婴幼儿用品和智能厨电密封件。
三、成型工艺:从规模化到超精密
多物理场耦合注塑技术
电磁辅助成型:通过磁场控制LSR分子链取向,提升特定方向力学性能(如弹性模量定向增强50%)。
真空注塑与压力反馈:实时调节模腔压力,消除微米级气孔,用于光学级LSR透镜(透光率>92%,雾度<1%)。
微纳尺度制造
微针阵列注塑:制造直径<50μm的医疗微针(如血糖监测贴片),突破传统PDMS的力学强度局限。
LSR与电子元件共集成:在注塑过程中直接嵌入柔性电路(如MEMS传感器),实现“结构-功能”一体化(案例:特斯拉电池组密封与应力监测集成模块)。
四、电子灌封:高可靠性的核心保障
高频高速场景适配
超低介电材料:介电常数(Dk)<2.8,损耗因子(Df)<0.001,满足毫米波雷达和6G通信设备需求(如信越的KE-1955系列)。
电磁屏蔽LSR:添加磁性粒子(如羰基铁粉),实现30dB以上的宽频段屏蔽效能。
新能源领域创新
电池包灌封:耐电解液腐蚀LSR(如陶氏DOWSIL™ CC-2588),用于4680电池模组密封,-40℃下仍保持弹性。
氢燃料电池双极板密封:耐氢脆、耐高压(>3MPa)的LSR方案替代传统橡胶,寿命提升至2万小时以上。
五、未来趋势:绿色化与智能化
循环经济驱动
化学回收技术:开发LSR闭环回收工艺(如热裂解再生硅氧烷单体),减少工业废料。
生物基LSR:以蓖麻油等可再生资源替代石油基原料(科思创已推出实验性产品)。
数字孪生与智能监控
IOT赋能产线:通过嵌入式传感器实时监测LSR硫化程度和应力分布,动态调整工艺参数(如恩格尔的iQ系列控制系统)。
区块链溯源:从原材料到终端产品的全生命周期数据上链,满足医疗和汽车行业的合规性要求。
结语
液态硅胶技术的革新已突破单一材料属性优化的范畴,转向与终端应用场景的深度耦合。未来,随着AI、量子计算等技术的渗透,LSR将向“自适应材料”(如温敏/形变响应型)和“能源-信息载体”方向演进,成为下一代智能硬件的基石材料之一。企业需重点关注 “精密化+功能化+可持续” 三位一体的技术布局,以抢占高端制造制高点。
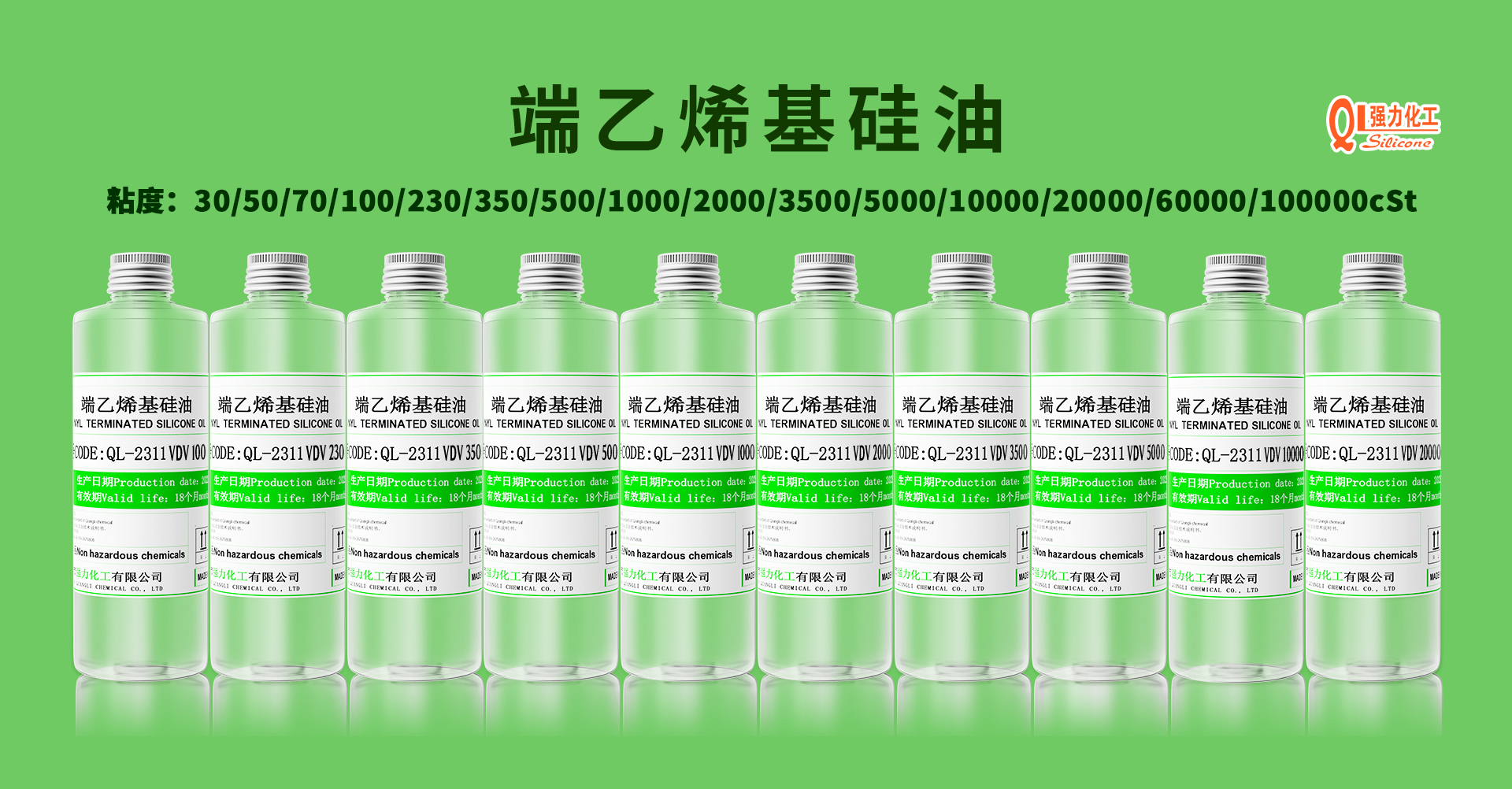